Software + Systems |
|
With MALAGA - the basic system -you can easily and purposefully develop the ideal profil - regardless of whether you want to create future-future-oriented structures from existing plants or design, simulate and implement completely new models for the greenfield.
Just as the primary goal is always to link the levels of information and process, we link all services from system engineering to integration testing to implementation and gain synergy from integration.
We offer an abundance of modular program units, which support you with your work effectively.
Software:
- MALAGA – Factory planning and logistics
- MASSIMO – Simulation
Planning is subject to increasing challenges (keyword: “turbulent environment, increasing requirements, more complexity”) and quick reactions are therefore required- and as well-future planning is agile (digital factory, IoT) and a response to the requirements for constant renewal and development of ratio potential.
This means: optimizing manufacturing processes and making the best possible use of resources from an economic and – increasingly important – ecological perspective.
|
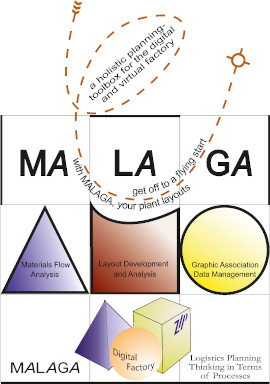 |
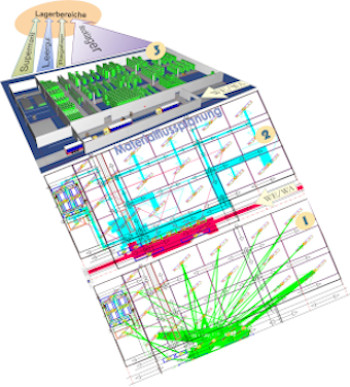 |
Materials flow planning
Everything starts with the materials flow - innovative processes are ensured by using appropriate optimization tools (example)
1 Material flow – direct connection Parameterized distribution and arrangement 2 Sankey diagram Material flow and logistics are the “timers” of production and therefore “strategic success factors” 3 Visualization At the end there is the virtual world In the digital solution with MALAGA, the planning technologies gradually intertwine - with largely automated planning “at the push of a button”!
|
We are always at the forefront of technology.
ZIP has received the prestigious elogistics award from AKJ Automotive. The main winners of the award were the automotive group Daimler and ZIP for the “Digital Logistics Planning”
|
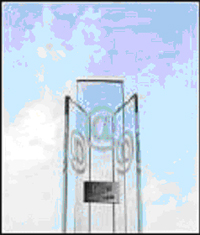 The elogistics award is presented for innovative logistics concepts and solutions that are already in use.
|
Factory planning
|
Malaga masters the implementation of processes in the layout at high speed. Individual goals are not optimized in isolation, but the range-spreading tasks are combined into a chain of rules and realised in the layout.
Single goals are not optimized in an isolated manner, The same maxim is valid also for the organization of the production areas - the manufacturing is developed process orientated as a whole.
The same maxim also applies to the design of the production areas - production is developed as a whole in a process-oriented manner. The program takes the data from the material flow analysis and uses it to develop the structure-in result: short planning cycles with a well-founded basis and the concrete evaluation of alternatives.
|
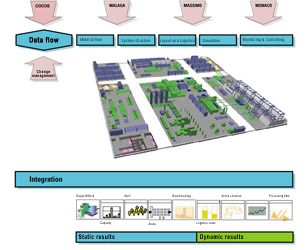 |
Logistics
|
In plants the concepts of lean manufacturing gain more and more influence. Due to that enterprises begin to re-consider the role of logistics.
The material flow and thus the supply and disposal become the backbone of manufacturing - and this heavily affects the factory layout. The aim is to keep stocks low and turn over quickly, so that the material flows and the supply rolls.
Structuring production using transport axes, on which the material flow is oriented, is an efficient part of MALAGA logistics planning. The focus on the continuous value chain and the perspective of process chain logistics force functional and transparent processes in the layout.
The concept of short throughput times is clearly reflected in the route navigation and information system Easyplanner
|
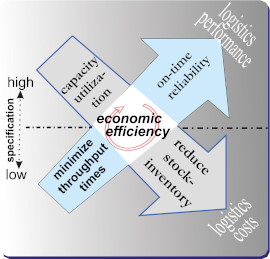 |
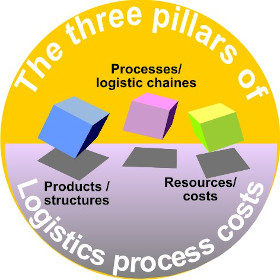 |
The immense increase and complexity of internal traffic requires relevant know-how in the area of logistics and layout systems. And only those who have the necessary information can foresee, plan and act accordingly.
MALAGA provides this information and supports the planner in many ways. Route capacities and bottlenecks are displayed, material flows are planned and controlled according to specified rules. Finally, the simulation shows how the planning can be successfully implemented into reality.
|
MASSIMO - Simulation convinces
|
MASSIMO (MAterialsflow System SImulation and MOnitoring) is a simulation package, that runs directly in the factory layout. All necessary data are already available anyway.
A powerful solution - the coupling of simulation and animation directly with the CAD. Lengthy model development and extensive data acquisitions are no longer necessary. Simulating at the"push of a button" is literally “easy”!
|
|
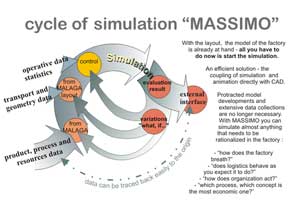 |
Simulation provides detailed results
MASSIMO finds saving possibilities and, -above all-helps to increase the efficiency of the system and optimize production.
Through simulation, dangerous undercapacities or expensive overcapacities in some areas of production plants can be reliably and promptly identified in the planning phase, even under dynamic load conditions. The simulation can be used to identify the effects of disruption-related problems in the materials flow. In this way, high usage losses in linked systems can be prevented. The simulation shows ways in which an increase in throughput can be achieved through organizational or control measures, thus avoiding expensive plant engineering solutions.
The strategy is to regulate and rationalize the organization of workflows and processes in production.
|
Requirements for the planning system
|
MALAGA challenge
Solution concepts are needed for “turbulent environment, increasing demands, more complexity– rapid reactions are required.
Future planning is agile (digital factory, IoT) and a response to the need for constant innovation and development of rationalization potential, e.g.:
Optimization of manufacturing processes and optimal use of resources from an economic and – increasingly important – ecological perspective.
|
Digital factory planning
No more patchwork software, but planning all in one piece One interface – one language – one planning system Data consistency along the entire value chain
|
|
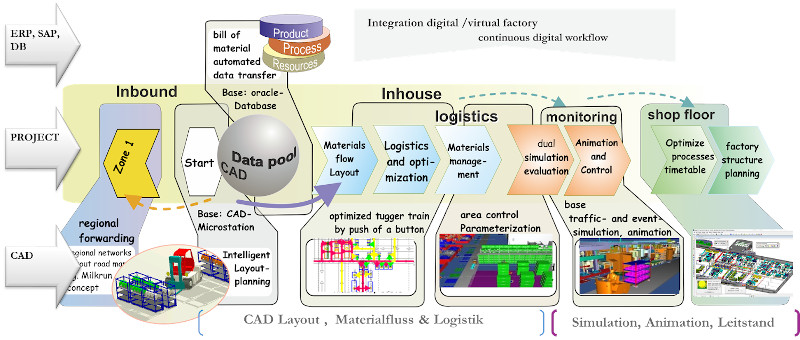 |
|
Solution MALAGA
- The digital factory and the associated innovations are therefore essential. MALAGA offers a comprehensive approach with a common database and consistently linked tools, methods, and models.
- The implementation of digital factory planning means building a digital foundation
|
key words
- Logistics planning, materials flow planning, /simulation/ monitoring/animation, layout planning & process planning, factory structure planning
- Convenient planning process at the touch of a button, more automation, better coordination
- Benefits: flexible, innovative, transparent
- High potential for efficiency, high cost-effectiveness
|
|
|
|
|
|
|